How Custom Machining is Shaping
the Future of Modern Manufacturing
When you need custom manufacturing, there should not be any limitations except the imaginations of your product designers and engineers. The ability of modern custom machining makes it possible to precisely manufacture nearly any item, including individually machined parts, the mold for other parts, or a part that holds other parts that require further machining (i.e., workholding).
Early versions of CNC machining date back to the 1940s. But this technology really took off in the 1980s and 90s. Since those early days of CNC custom machining, the technology has continued to evolve, with improvements like 5-axis machining, automation and robot integration, and better human operator training.
The manufacturing landscape is changing. Worker shortages and increasing product demand are causing manufacturers to look at different ways to produce products more efficiently. But “faster” doesn’t have to mean “less accurate.” With the right tooling solutions in place, manufacturers can improve manufacturing processes exponentially. And with the right tooling partner, manufacturers may be able to achieve unmatched levels of precision and accuracy.
How is custom machining changing the shape of modern manufacturing?
1. It improves worker safety.
Today’s workforce demands—and deserves—a safe work environment, and companies should strive daily to ensure employee safety. Machining processes are automated according to the preset programming. This reduces labor intensity, exposure to potentially dangerous equipment, and the chance that something can go wrong. With comprehensive training and proper safety precautions in place, human operators have very little risk of injury, or even discomfort. Ergonomics—creating, maintaining, and establishing a workspace environment that fits within the comfort and safety needs of staff—leads to machining consistency and precision.

2. It enhances quality control.

Quality control is everything in a modern production process. Manufacturing processes must be repeatable at high speeds and high efficiencies to ensure product consistency. If one surface has a burr, or one measurement is off, the entire production process can be compromised. Modern manufacturing has to be able to keep up with increased demand and higher quality standards of consumers and businesses. With a custom machining partner, manufacturers can ensure that tooling solutions are not only unique to their processes, but as efficient—and accurate—as possible.
3. It creates an environment for innovation.
When businesses want their products to stand out or need manufacturing solutions that are unique to their proprietary production process, custom machining is essential to success. Your company creates products that can’t be found anywhere else, so why settle for off-the-shelf CNC programming? Partnering with an outside custom machining expert frees up in-house engineers to further innovate, and designers to remove all boundaries from their imaginations. When the limit is your imagination, the possibilities are endless. Everything from medical device innovations to new car concepts can be created, knowing that prototypes, parts, and production equipment can be precisely engineered and produced.

Need an Expert?
Need the Proof?
4. It improves precision and accuracy.
CNC stands for “computer numerical control,” and like the name suggests, it relies on computers and pre-input programming to control parameters and ensure the accuracy of the CNC machine can be guaranteed. This prevents differences in product quality and reduces the impact of any human factors. As the manufacturing sector continues to adjust to the changing workforce, CNC machining and custom machining solutions will become increasingly important for accurate and repeatable processes. A sophisticated machining partner like Ahaus goes even further by employing the use of cutting-edge testing equipment and climate-controlled environments to achieve levels of precision that were previously unattainable.
5. It optimizes resources.

The labor shortage is real and the competition for employees will not be going away. Companies are having to do more with fewer resources. When your project has a reliable custom-built machining solution as a part of the production process, your people can focus on other important factors, removing activities that aren’t value-added. In addition to maximizing human resources, expertly designed and machined production components can minimize waste of raw materials. Together, increased employee efficiency, minimized downtime, material waste reductions, and lower rejection rates means you are getting the most out of all of your resources.
A Hammer, a File, a Lathe, and a Mill
Working with a machining partner such as Ahaus will grant companies access to a vast range of machining capabilities, including high speed machining, 5-axis machining, and conventional 3-axis machining. With 35 CNC machines and full capabilities for production machining in our Richmond, Indiana facility, Ahaus is fully equipped from a technology and equipment standpoint and has a history of adapting with the times to prepare for the future of manufacturing.
“My grandfather said, anything you can do with a hammer, a file, a lathe, and a mill, we can manufacture at Ahaus, and that was in the 40s,” said Kevin Ahaus, Ahaus Tool & Engineering president and co-owner. “We were the primary supplier for the components that made the IBM Selectric typewriter ball back in the 60s and early 70s. We’ve since developed into a high precision machining company. Today, every day we’re producing products coming off our CNC equipment with 6,000, 10,000, 15,000 RPM spindles, all the way up to 5-axis machines.”
The technology behind CNC custom machining has evolved significantly since the 1980s. You can perform jobs much faster than you could have even ten years ago. It is particularly the machine and cutting tools—as well as automation capabilities in general—that have become so much more efficient, leading to a greater proficiency in manufacturing overall.
Ahaus is not just focused on staying ahead of the technology curve. Our team has broad and comprehensive training and experience that is unmatched in the industry. Our internship and apprenticeship programs, turning out the future of machining experts for four decades now, produces machinists that are not only skilled in the latest CNC technology, but are armed with an intimate knowledge of foundational machining principles.

Ahaus even goes so far as to start our newest interns on traditional manual machining tools to ensure that our employees have a feel for the work that goes far beyond technical operation. Some of our most senior team members started in the internship or apprenticeship program over 30 years ago and have witnessed firsthand the evolution of the machining industry. The collective knowledge of our experienced machinists, designers, and engineers paired with our commitment to developing new talent gives our clients access to a resource that can’t be found anywhere else.
With the constant evolution of manufacturing, it is imperative for companies to have a tooling and engineering partner that is committed to the education and development of its workforce and the adoption of innovative technologies, processes, and operational philosophies. Ahaus is extremely proud of its history of human and technological innovation and is committed to continuing to lead the way forward in the custom machining field.
The Relationship Factor
At Ahaus, we go beyond custom machining; we are in the business of relationships. We want to get in on the ground level to understand your products, your goals, and your measurables so we can provide a long-lasting machining solution that solves problems today, tomorrow, and in the long-term future.
“When we get a new project with a new or existing customer, the first thing we do is hold it to our vision statement of being the most highly sought-after partners in the industry,” said Eric Partin, Ahaus project engineer. “We provide weekly communications; we’re as transparent as possible with the status of how things are progressing, taking some of the pressure off of the customer.”
We are a company that knows what it feels like to have people counting on you. So, when you need a machining partner who can deliver results, you can count on Ahaus. You are the expert on your projects, and our engineers are machining experts, guiding you through the machining process.
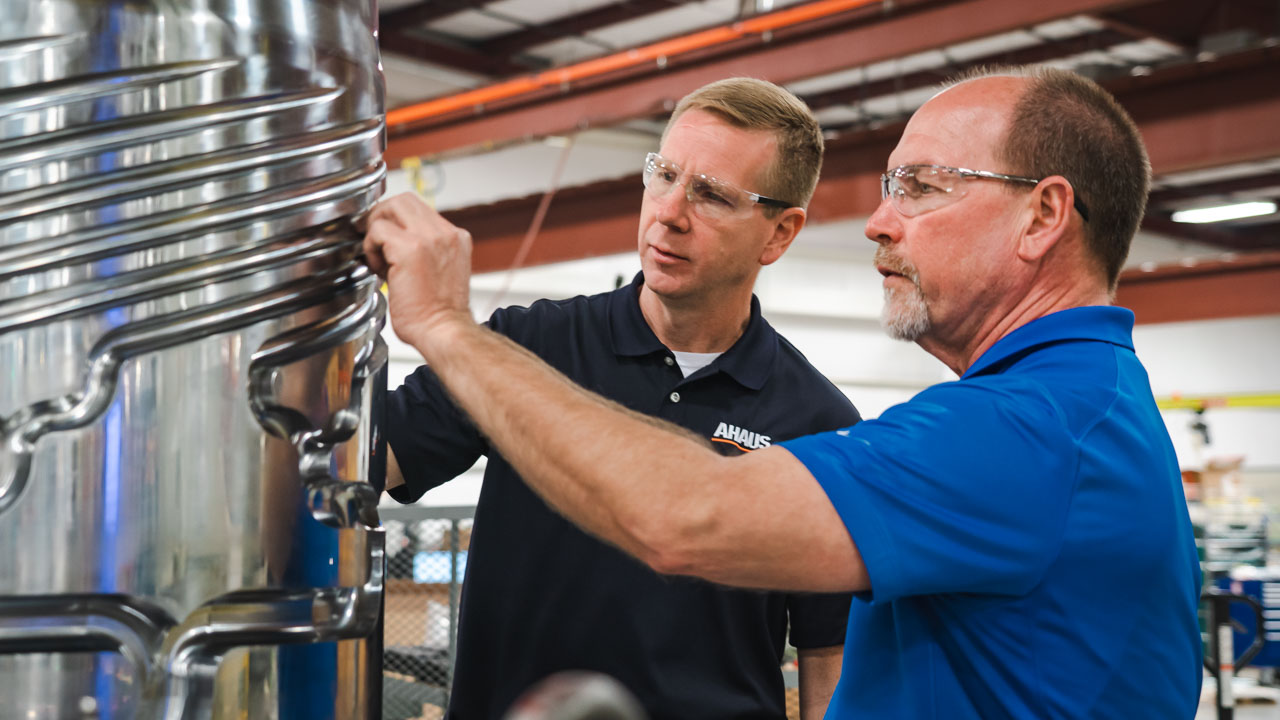
We assess your machining needs, including tolerance and correct tooling, and communicate with you through our dedicated project engineering team members until your parts are delivered.
The Future of Custom Machining
As companies adjust to the labor shortage and continue to provide more attractive workplaces that ensure workplace safety and ergonomics for employees, the need for custom machining solutions will continue to increase. Production workflows are all unique, and sometimes proprietary, requiring a machining partner who provide manufacturing solutions individually tailored to custom specifications.