Heat Exchanger Systems & Equipment
HEAT EXCHANGERS · RADIATORS · EVAPORATORS· CONDENSERS
The heat exchanger industry provides the comfort we have come to expect in our homes, businesses, and driving in our cars. The manufacturing processes for heat exchangers requires critical processes to ensure proper assembly, leak-free joints, and consistent quality.
At Ahaus, we have provided special machines and automation for over 30 years to help the heat exchanger industry produce radiators, heater cores, evaporators, condensers and other heat exchangers. We have also brought to life special machines, leak testers, and automation systems to integrate these heat exchangers into many small and large subassemblies.
Need an Expert?
Need the Proof?
Precision Required in Radiator Assembly
No car or truck would get very far without having a mechanism to keep it from overheating. Heat exchanger technology suits that very purpose. Heat exchangers come in a wide array of configurations and use a variety of methods to transfer and dissipate heat to keep hard-working machinery cool. In the case of an automobile or truck, an inadequate or faulty cooling system can be responsible for serious damage to an engine.
Heat Exchangers for Vehicles
The “heat exchanger” within a car or truck is the radiator, which is at the center of a motor vehicle’s cooling system. A radiator within a vehicle is an air-to-liquid style heat exchanger constructed of materials such as copper, brass and aluminum.
The basic operation of a vehicle’s cooling system consists of a liquid coolant that is pumped throughout the engine to absorb the heat that it produces. The coolant then makes its way to the radiator, where it courses through a series of tubes and is cooled by a combination of fans, ambient air flow and heat-dissipating “fins.”
Precision Required in Radiator Assembly
With the cooling requirements of the high performance engines that we have today, radiators are built for maximum durability and efficiency. From the heavy, leak-prone “round tube” and “honeycomb” designs of the past, radiators have evolved into sturdy-yet-lightweight apparatuses.
Just as most other manufacturing systems and methods have been refined over the years, the assembly of radiators and radiator equipment is no different. With the assistance of computer-aided design (CAD) programs, automation equipment is often used in the construction of the modern radiator. Advanced crimping equipment, fin mills and radiator core building machines are more precise and consistent than ever, producing a generation of dependable, long-lasting radiators.
The features and functionality of internal combustion engines continue to progress. And the engineers behind the development of the cooling systems are meeting all challenges in order to keep pace.
Word-Class Products
Utilizing the latest versions of 3D modeling software, Ahaus design engineers can bring quality equipment to life in very short lead times. For our customers, this results in world-class products that will last for years, including standard core builders, fin mills, tank crimpers, and leak testing machines. Capabilities range from heater cores to large truck radiators and lean manufacturing to automotive matrix assembly.

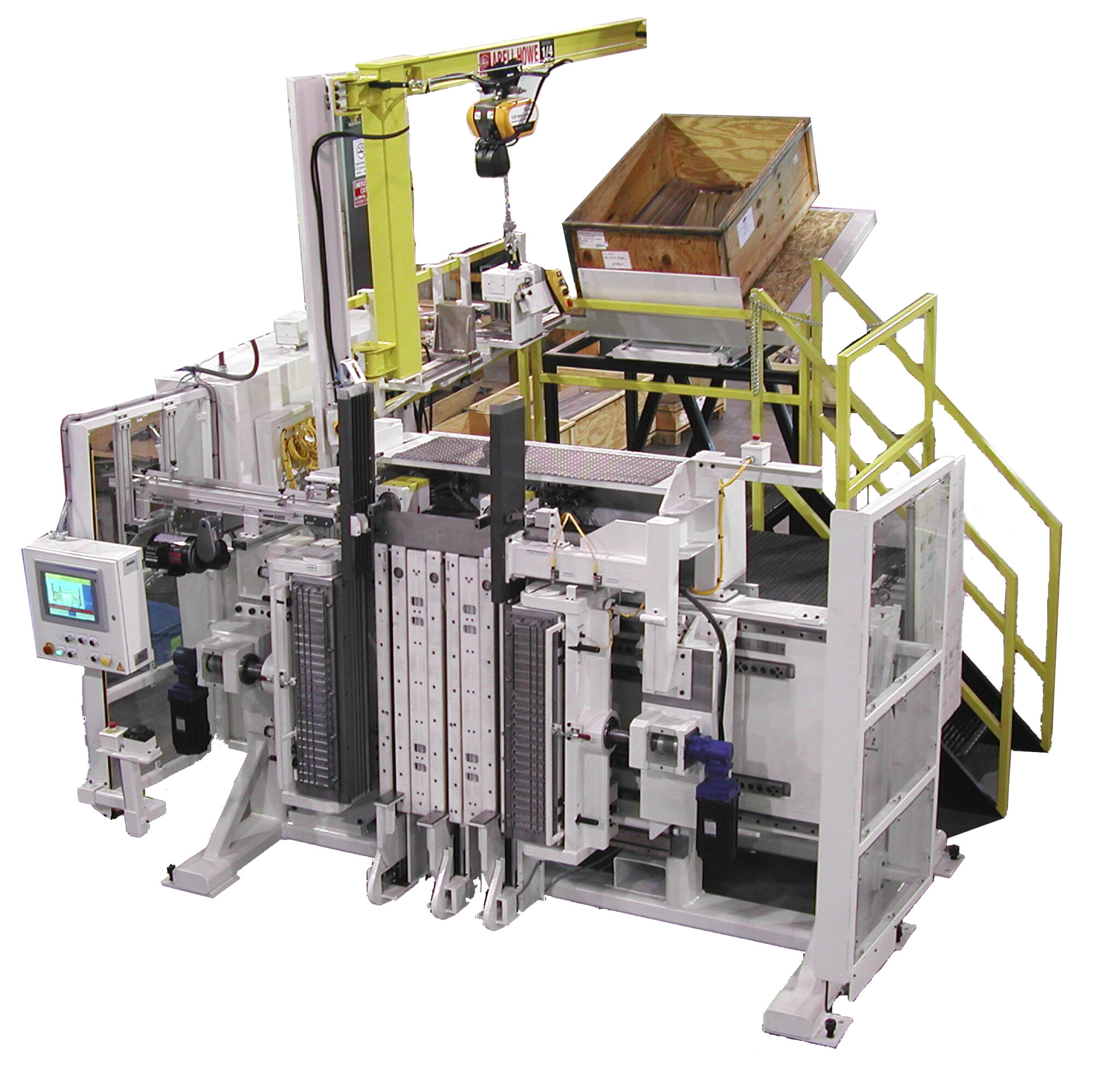
Complete Systems
Ahaus can provide complete heat exchanger manufacturing systems or components, including:
- Crimp dies and presses
- Modular crimping
- Core builders, semi-automatic and matrix
- Leak test equipment
- Full assembly or robotic systems
- Fin mills
“Ahaus understands what the potential problems are so they can get right to the heart of the issues. We benefit from foresight rather than hindsight when working with Ahaus.””
SENIOR MANUFACTURING ENGINEER
Worldwide Leader in Thermal Management and Heat Exchanger Products